CALCULATED, COMFORTABLE, COST EFFECTIVE, CAREFUL DESIGN, CERTIFIED
The result we all want is a comfortable cost-effective building. With careful design and detailing this is not too difficult to achieve. However both the performance and cost-benefit of every element needs to be calculated in advance.
We use the following comfort criteria:
Internal temperature never below 20 deg C
Internal temperature never above 25 deg C for more than 10% of the year.
Surface temperatures never more than 4 deg different from air temperature – no cold spots (“thermal bridges”) to induce condensation or air currents.
Air quality never below international health standards.
No drafts or uncomfortable air currents.
Very low energy use, a small fraction of typical energy use and generally so low that no heating system is required.
This can be achieved with almost any style and type of construction. The differences from a standard building are very slight because they are in the design, calculation and quality of the construction phase.
For the Designers this means that every aspect of the energy balance must be calculated to ensure that the losses (through the thermal envelope) are not too much greater than the gains (from the sun, users, equipment and heat recovery ventilation).
For the Builder this means that the construction must be carried out carefully in accordance with the design generally and in particular that the airtight thermal envelope is not breached without being repaired (an air leakage test is carried out once the airtight envelope is complete but before finishes are installed so that any leaks can easily be sealed).
In practice there are some extras and some savings.
The main extra considerations are:
Windows: Orientated and shaded for optimum heat gain/loss. Double glazing with reasonable quality frames.
Insulation: Slightly higher than standard insulation levels average U Value of whole envelope about U0.25 (R4) - usually it is most cost effective to have higher values in walls and roofs and lower in floors and windows. Now that high grade insulations are economically available in Australia, achieving these levels is no longer difficult or expensive.
Airtightness: Vapour barrier sealed airtight at junctions.
Ventilation: Whole house balanced ventilation system that allows recovery of otherwise wasted heat.
The main savings are:
No heating system and therefore no Gas connection.
No extract fans.
No ceiling fans.
Fewer opening windows.
Simpler wiring.
Zero heating bills (less than zero with optional photovoltaic contribution)
Calculated
There are many calculation tools such as international and national standards (ISO, AS, BS, DIN etc.) which can be applied to various aspects of buildings but in general the design of small scale and domestic construction relies on convention (or unsubstantiated claims) and is not subjected to comprehensive analysis that can predict its performance. Innovation is avoided because its results are unpredictable. Completed buildings are rarely checked to verify that they comply with the claimed design performance. This can cause disappointing results and additional expenditure without commensurate benefits.
Calculation tools:
PHPP (Passive House Planning Package)
The PHPP provides a design tool that coordinates the relevant international standards and data necessary to accurately predict building performance (all building types, not just houses). Its accuracy has been verified by decades of monitoring real buildings designed using the PHPP. Every relevant physical aspect of the design can be input and each can be varied to compare the effect of the changes.
The PHPP provides detailed outputs on every aspect of the physical performance.
A 90 second video on Passivhaus can be seen at: https://www.youtube.com/watch?v=CasrjYhZB1M
A general description of PH principles is available at: http://passivehouseaustralia.org/what-is-passive-house/
For a detailed description the PH brochure can be downloaded at: http://www.passivehouse-international.org/index.php?group=1&level1_id=70&page_id=286&lang=de
The key data is:
Annual energy use per sq m for all uses including Heating, Cooling, Domestic Hot Water, Lighting, Appliances and equipment. CO2 emission form energy use. These can be translated into running costs with an energy cost calculator.
TYPICAL RESULTS FOR PASSIVHAUS CONSTRUCTION
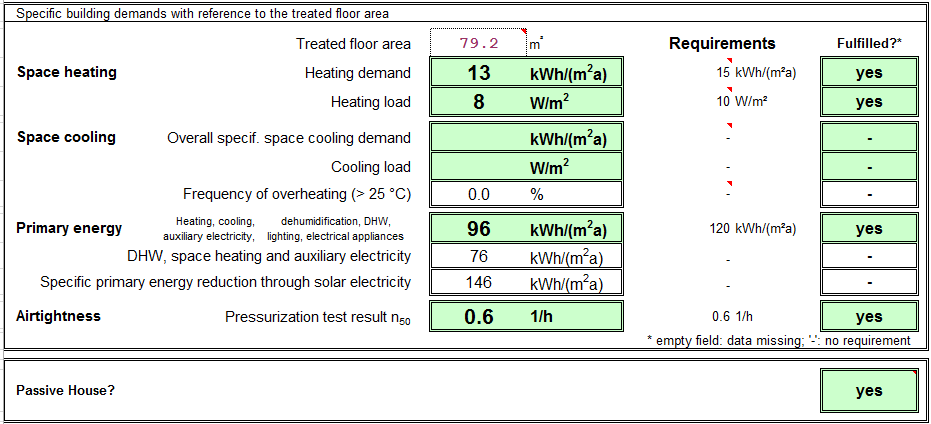
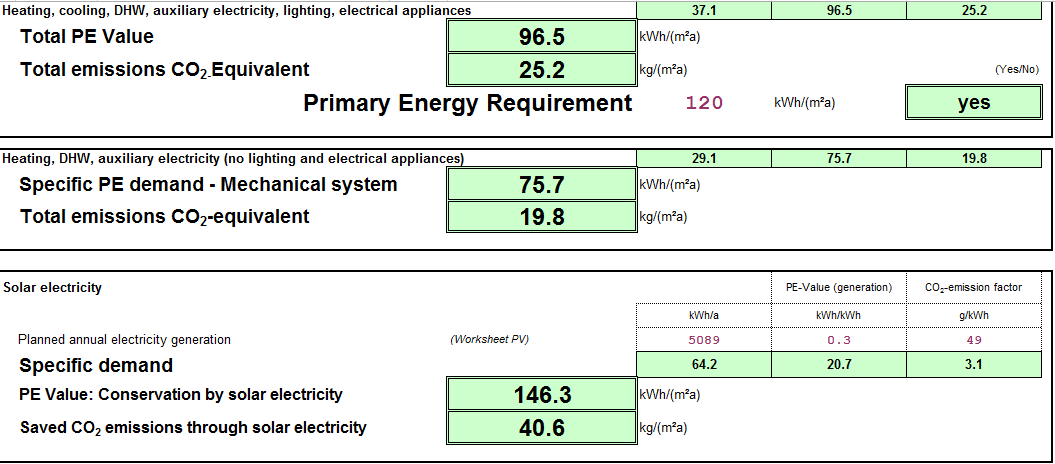
Total emissions 25.2 kg/m2 of CO2 per annum before savings from solar power.
Saved emissions due to solar electricity = carbon positive by 40.6 kg/m2 of CO2 per annum For a typical 200sq m building this equals minus 8 tonnes of CO2 per annum.
TYPICAL RESULTS FOR STANDARD CONSTRUCTION
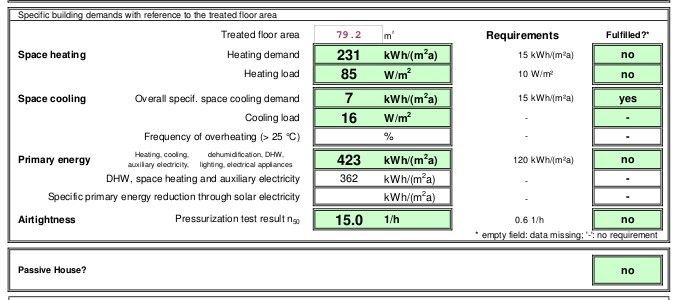
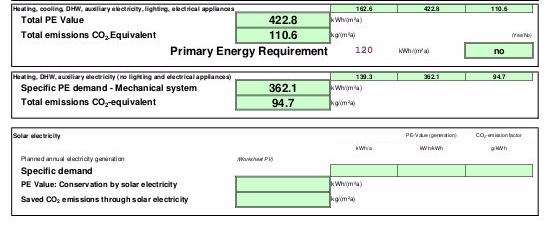
Energy required to remain within the min 20 to max 25 deg C comfort range for an identical building but using typical construction standards However the CSIRO report found that few standard houses are capable of remaining within the comfort range because the demand is greater than the heating/cooling equipment can provide. The actual energy use is therefore limited by the maximum capacity of the heating/cooling equipment. Refer to the CSIRO report for measured energy uses of typical houses.
Carbon emissions 110 kg/m2 of CO2 per annum
For a typical 200sq m building this represents emissions of 22 tonnes of CO2 per annum.
The PHPP also demonstrates the effect on energy consumption of air loss due to changing the level of air leakage. Air leakage can also reduce the effective R Value of insulation by more than half but this loss in insulation value needs to be calculated separately.
The PHPP is an internationally applicable tool that allows local climate data to be used, but in some climates supplementary calculations might be necessary to describe the effect of short-term extremes that are not accounted for in average climate data.
Energy cost calculator:
Since the PHPP provides data on the energy use for each type of fuel that the design calls for, this can be translated into a monetary value using readily available cost data. This can be expressed both as running costs per year and present capital value of future running costs over the life of the building.
By comparing this with an equivalent standard building the financial benefit in terms of energy use of every change in the proposed design can be demonstrated. This will be independent of capital cost which may be subject to other factors but the even so, the present value of the energy savings can be expressed as equivalent to a capital saving.
Capital cost calculator:
Unlike most domestic and small scale designs, the PHPP process requires the relevant building elements to be quantified. These quantities can be output as schedules of the elements which will be updated with every variation of the design. This helps with estimating the cost of each element.
Data from a recognised source can be used as the primary database to create a basic cost plan for the proposed design and the equivalent standard building. The effect of variations in the construction can then be investigated using the standard data independent of builders mark-up. Ultimately builders can also use the quantities provided by the PHPP output to calculate their own prices.
Comfortable
Occupant health, safety, and comfort standards have been widely studied resulting in a variety of standards that have been coordinated in the PHPP method. The basic requirements are that the interior remains between 20 and 25 degree C at least 90% of the year but it includes many other requirements for such things as air quality, surface temperatures and condensation control. The PHPP parameters are based on providing optimum conditions for occupant comfort, health and safety. These can be compared with studies of the actual performance of equivalent standard buildings.
Other than air temperature the main factors that affect occupant comfort are:
Differences between the temperature of surfaces and the occupants’ body - causing radiant discomfort.
Differences between the temperature of surfaces and the air temperature causing air movement discomfort and surface condensation.
Uncontrolled air leakage which can create multiple problems including reduction in effectiveness of insulation, escape of heated or cooled air, condensation within the structure and draughts.
Poor air quality caused by ineffective ventilation that fails to remove contaminants and replace them with clean air.
COst effective
Many problems can be solved by throwing money at them but this is seldom a reasonable approach. The objective should be to save money by using cost-effective methods of reducing running costs. The calculation methods already described allow the cost-benefits of each proposed strategy to be realistically assessed over an agreed building lifespan. In general the most cost effective methods are those that serve more than one purpose. For example Structural Insulated panels can serve up to five functions in a single product.
The PH standard requires maximum heating/cooling demand 15kWh/m2 per year or maximum peak load of 10W/m2. This is less than the hot water demand and is tiny by normal standards. It is easily supplied with simple equipment and can be powered by p.v. panels which would make it zero running cost. The maximum permitted electrical use is 120kW per year which is also tiny. Savings on running costs can be converted into a capital value which is far greater than any additional costs for higher standard construction. Large scale studies in Europe show that the PH construction costs between 3 and 8% of the total cost which is much less significant to the budget than the variation in the costs that choices in finishes and fixtures can make. In many parts of Australia the reduction in cost of the heating system the Passivhaus permits could outweigh the additional costs of Passivhaus construction. On an average home, a well-planned Passivhaus can save over $2000 per year on running costs. If this was put into repayments on a typical mortgage it would be equivalent to around $60,000 saving at todays’ rates. On some houses the savings could be double this.
Careful construction
This detailed design process allows the elements that are critical to the buildings performance to be clearly identified. In particular, elements that may not be well understood such as heat recovery ventilation and methods of preventing air leakage or thermal bridges need to be well detailed and monitored. The benefit of being able to calculate the overall cost-benefits and comfort-benefits is that construction methods appropriate to the particular job can be investigated and the vagaries of relying on conventional wisdom can be overcome.
To achieve the desired comfort levels in a cost-effective way requires collaboration between the design and construction processes.
Almost any form of construction can be made to work as long as it is carefully detailed with no breaks in the insulated envelope and it is carefully built so that there is minimal air leakage.
Insulation: Only moderate insulation levels are required (about 25% higher than Building Code requirements) and since insulation is one of the least expensive elements of construction it usually doesn’t have much effect on overall costs.
Windows: Decent window frames are required with reasonable insulation properties and airtightness but for Australian climates they only need to be double glazed not triple glazed.
Heat Recovery Ventilation: As well as recovering the heat from the air before it is expelled it also guarantees proper air quality even if windows remain closed on very hot or very cold days. This means that fewer opening windows are required which saves costs. The efficient design also means that minimal heating and cooling is required which means that the Heat Recovery Ventilation pays for itself.
Air tightness: Air leakage significantly reduces the effectiveness of insulation and has multiple impacts on occupants comfort. This is one of the principle reasons why constructed houses do not live up to their star rating. Some construction methods are inherently air tight and just need sealing at junctions. For other systems such as timber framing, the vapour barrier needs to be taped at all junctions to form the air tight layer. The cost of the materials required to prevent uncontrolled leakage is very small, the significant factor is that they must be installed correctly and carefully. All insulated construction should have a vapour membrane so the extra work is in sealing this airtight. The recent CSIRO studies found that average new houses have an air leakage rate of about 15 to 20 air changes per hour. By taping the vapour barrier airtight at all junctions this can be reduced to below 0.6 air changes per hour which is the Passivhaus standard.
CERTIFICATION
Unlike most standards, Passivhaus construction can be certified. This means that an independent Certifier accredited by the Passivhaus Institute will check all the construction design details and calculations to ensure that they will provide the required comfort conditions and energy levels. An air leakage test must also be provided before a PH Certificate is issued. The certificate provides the owner with certainty that they will get what they expect and is also a valuable asset when the property is sold.
The Passivhaus Institute currently charges about $3000 for the certification process although this varies with the exchange rate and an air leakage test costs about $500.
HOW CAN THE COMFORT & ENERGY LEVELS BE ACHIEVED COST EFFECTIVELY?
When comparing cost effectiveness of alternative house design the benchmark is a standard 6 star house required by the Building Code. On paper a 6 star house must provide the stipulated standards of protection from heat loss and gain. Unfortunately, in practice 6 star houses do not necessarily meet either the comfort or energy use standards which theoretically they should. The CSIRO therefore carried out a wide ranging study of the actual performance of houses built to star ratings which is available from the CSIRO website.
The gist of the report shows that the built houses rarely achieve either the intended comfort levels or energy use levels. There may be a variety of reasons for this but the most obvious is that the Building Code of Australia (unlike the UK Building regulations) has no requirements for air leakage or thermal bridges. The effects of air leakage are described separately in more detail but put simply the result is a dramatic loss of insulation value.
Because people are paying more for the insulation etc. required to achieve 6 star rating but not getting the improved comfort and lower energy bills expected this has led to an unfortunate dissatisfaction with idea of increasing insulation levels.
Insulation levels:
The insulation levels required for a Passivhaus need not be very different to those required for a 6 star house. The difference is that in a Passivhaus house the insulation must be designed and installed to work effectively. This is achieved by details that eliminate thermal bridges, and an air tight vapour barrier that prevents condensation within the structure or air movement that reduces the value of the insulation. Without these the insulation can lose as much as half of its effectiveness which means that you are paying for insulation and only getting half of the value. Proper detailing and an air tight vapour barrier are therefore extremely cost effective. Although they are mandatory in Europe, they are not part of standard Australian construction and there is therefore a learning curve to be overcome. Construction methods that are easy to seal can help with this.
Insulation is one of the cheapest elements of a building and ranges from $2.50 to $14 per R per square metre depending on the type and application. As a comparison, floor finishes range from about $75 to $175per square metre. The choice of floor finish will therefore have a much bigger impact on cost than the level of insulation. Increasing the insulation level of the thermal envelope is therefore very cost effective and brings long term comfort benefits as well as allowing cost reductions elsewhere. The CSIRO study found that the Melbourne houses used over 100kWhours per square metre per annum and still didn’t achieve the minimum comfort standards. To achieve the minimum comfort standards they would have to use about twice as much energy but this is usually beyond the capability of the installed heating/cooling equipment. Minimum Passivhaus standards will achieve the required comfort levels with a fraction of the energy (max 15kWh/m2/annum). This is low enough to be provided by a cheap reverse cycle split system which can be powered by a medium sized photovoltaic array. By spending a few thousand dollars extra on effective insulation this can be reduced even further to about 5kWh/m2/annum which is one twentieth of the levels measured by the CSIRO. This is so low that very little needs to be spent on heating/cooling equipment and the electricity required can easily be provided by a very small photovoltaic array resulting in zero energy bills. When demand is reduced to these levels the heated/cooled air can be distributed by the Heat Recovery ventilation system so no other heat emitters are required.
Effective insulation is the cheapest way to save on heating equipment and energy bills while gaining on comfort.
Thermal mass is particularly beneficial in SE Australia where there are commonly rapid temperature fluctuations of 20 or even 30 deg C. Although thermal mass is taken into account in PH calculations, it is not essential because the maximum temperature swing in a PH design is 5 deg C. Thermal mass can often be provided cost-effectively when it serves more than one function such as by using a concrete slab or masonry internal walls. Externally insulated concrete, masonry or earth systems can often provide air-tightness, fire resistance and structure as well as insulation and thermal mass.
Glazing:
Windows are an important part of the thermal envelope so they need to be considered in the same way as insulation. At one time double glazing was a foreign concept but this is no longer the case so decent double glazed windows are not only essential to comfort but also cost effective for the same reasons as insulation. The choice of windows available in Australia that provide the necessary insulation values grows daily and even very high quality European frames are now competitive.
Although Passivhaus design does not rely on passive solar gain, the sun is such a valuable source of energy in this country that by using it sensibly the heating/cooling requirements can be dramatically improved. This is described in more detail separately.
Air Quality
Removing damp and smelly air from bathrooms, kitchens, toilets etc.is already an accepted cost in any new house. Heat Recovery Ventilation replaces this and takes it a couple of steps further. Recovering the energy from the air before expelling it reduces running costs and can reduce or eliminate the cost of an additional heating system. Providing controlled levels of filtered fresh air to the living areas ensures a level of air quality that is impossible with uncontrolled ventilation. Dust and pollen is filtered out and it can allow windows to remain closed during very hot or very cold weather. Fewer opening windows are required which can reduce costs and allow more versatile plans where natural cross ventilation could not be achieved. Natural ventilation often requires high level windows with costly remote operating gear which is not necessary when using HRV. The choice of HRV systems available in Australia is increasing so competition is making them even more cost effective.
General construction requirements
Most kinds of construction and any architectural style can be made to work to Passivhaus standards as long as it is carefully detailed to provide thermal bridge free, air tight insulation. Some methods are easier than others but since the cost of a house is fundamentally dependent on what Builders perceive to be the cost of constructing it, the method that most suits the particular builder will be the most cost effective choice. Typical timber framing can work but it needs to be lined with an air tight vapour barrier on the inside and sufficient continuous insulation on the outside. Many “systems” have the benefit of trained builders who understand the costs and techniques involved.
Efficient planning: If you want to get the most for your money, the plan needs to be as efficient as every other aspect of the design. Plans can vary as much as 30% in the amount of non-habitable space. At typical build costs this can represent tens of thousands of dollars or the space can be used to enlarge the living areas within the same floor area. By efficient design, the same accommodation can often be provided in 20 to 30% less than the standard floor area without making the house feel less spacious.
Minimising the ratio of surface area to floor area reduces the amount of material needed for construction which is another saving in capital cost. Compare these 100m2 footprints:
5m x 20m footprint on one floor gives 100m2. Perimeter 50m. Slab area 100m2. Insulated Roof area 100m2 Wall area 120m2. Roof & wall area to floor area ratio 2.2 to
7mx7.1m footprint on 2 floors gives 100 m2. Perimeter is 28.2m. Slab area 50m2 Insulated roof area 50m2 Wall area 141m2. Roof & wall area to floor area ratio 1.91 to 1
Even on this small house example, the 30m2 of reduction in wall and roof area at typical rates could be worth up to $10,000 on the construction cost (however some builders might charge a premium for 2 storey construction).
For the same reason this is also usually the most thermally efficient form because heat transfer is approximately proportional to surface area. This provides a saving in running cost. However, because solar gain is such a significant factor in Australia, long narrow plans which allow all rooms to have solar access can be beneficial on thermal grounds. In climates further from the equator with less sun, the additional solar gain would not be enough to compensate for the additional surface area. Multi storey construction is more thermally efficient because roofs are the greatest contributor to heat loss and gain - although roofs are usually the cheapest element to insulate. Terraces and apartments have even less external envelope and are the common urban solution in cold climates.
In urban areas where land is at a premium, compact plans are even more important because they free up ground area. Of course cost and energy savings are not everything and there are many reasons why a particular design might need to diverge from the optimum cube - such as orientation, views, site shape, access, slopes etc. Where land is not an issue, very few designs will end up close to being a cube but it is good to consider the advantages and disadvantages of each decision to move away from the most efficient form. In Australia the effect of free solar energy is much more significant than the efficiency of the volume so locations with good solar access can easily be long and narrow instead of compact.
CONCLUSION
Australia has the advantages of plenty of sun, benign temperatures and large amounts of land which permit optimum orientation. If Northern European countries with none of these advantages can legislate to make all new buildings zero carbon there is really no reason why Australia cannot do better.